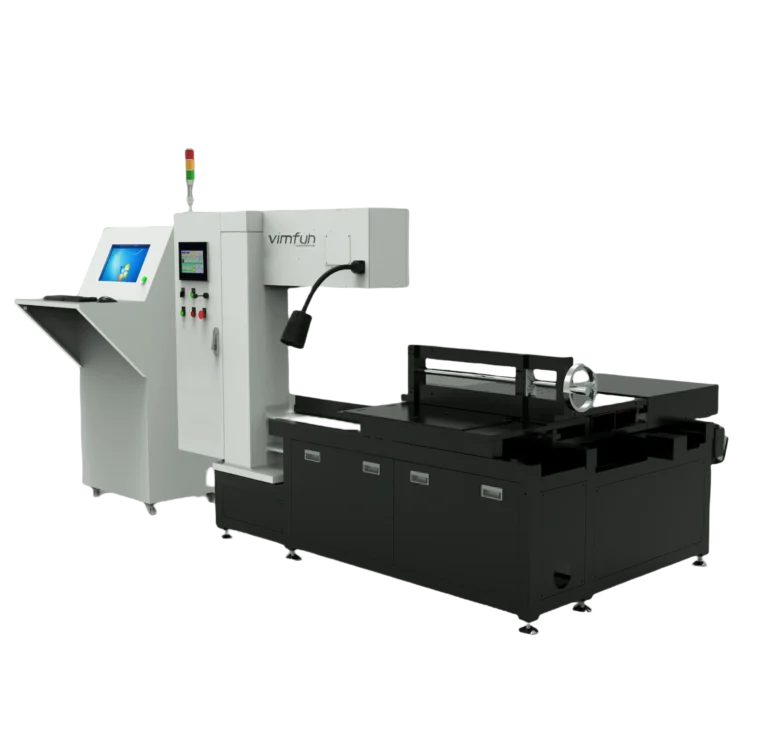
Simple for Complex Cuts: Graphite Inner Profile Cut Machine
If your job includes cutting shapes that are hard or have many sharp turns and lines, this Graphite Inner Profile Cut Machine is the perfect tool to help you. It can quickly cut inside curves, small holes, and narrow parts. It is made simple to use, so you can focus more on your work and less on learning the tool. This cutter saves you a lot of time and gives you better-looking results by helping you do hard and tricky cuts efficiently. Works of a Graphite Inner Profile Cut Machine A CNC graphite inner cut machine is a tool that uses a computer to cut shapes in graphite. CNC stands for Computer Numerical Control. That means you give the machine a shape design using a computer. The machine then follows the design and cuts the shape precisely. It is the same shape every time, with no mistakes. It is excellent